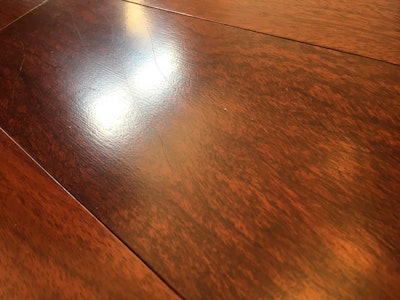
The Problem
I was called to inspect a prefinished ⅝-by-5-inch engineered Brazilian cherry floor due to small cracks in the veneer.
What Happened
The flooring was installed in March of 2014 in a home in the south-central U.S. It was glued over an existing concrete slab with a moisture vapor retarder underlayment and a polyurethane wood flooring adhesive. The installers tested the moisture of the slab with a moisture meter but did not take moisture readings of the wood flooring.
The customers first noticed the cracks in May 2016. The contractor looked at the issue and said it could be related to direct sunlight overheating the boards, as the cracked boards were adjacent to a wall of mostly windows. The contractor agreed to use leftover flooring to repair the affected boards, but by the time workers went to perform the repairs in December, the areas with cracks had expanded.
The Inspection
I inspected the flooring in June 2017, and the surface cracking was noticeable from a standing position throughout the installation. The cracks weren't uniform: They were at the ends of some boards, from end-to-end on others, and diagonally across some; some boards had a solitary crack.
The temperature averaged 75.9 degrees and the RH was 46.9%, which meant the wood's equilibrium MC was 8.7%. I tested the wood flooring MC in several areas; at a ¼-inch depth, it averaged 6.07%. At ¾-inch, it averaged 8.64%—within the normal EMC range.
RELATED: Engineered 101: Understand the Fundamentals of Engineered Wood Flooring
When I was there, the air conditioning was running. The customers said they did not use any humidification during the heating season. I looked up weather data to estimate what the indoor RH had been since the original installation. It showed that over the previous three years there had likely been 247 days when the RH in the home had been lower than the flooring manufacturer's recommended 35%–55% RH range, with 170 of those days at or below 25% RH. I checked the surface temperature of the wood flooring and found areas in the direct sunlight averaged 95.1 degrees while areas without direct sunlight averaged 72.3 degrees.
I determined the flooring in the home had been affected by low RH outside of the recommended range; this is considered a job-site-related issue.
How to Fix the Floor
The problem was so widespread that the entire floor had to be replaced.
In the Future
The customers in this case said that at no time did anyone advise them that they needed to keep their home within any particular humidity or temperature levels. Education of the customer is critical when selling an engineered product in an area that might experience low humidity.