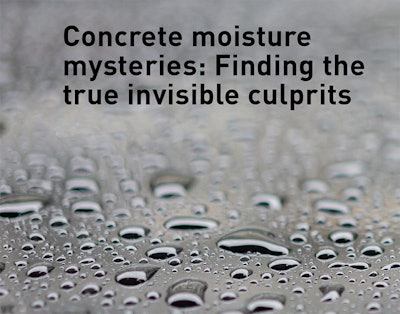
I have been involved in virtually every aspect of concrete waterproofing, from tunnels to bridge decks and substructures and literally millions of square feet of floors. One of the most frustrating aspects of dealing with the flooring industry is the amount of misinformation out there, particularly frustrating when it comes to moisture issues and the testing of moisture.
An article I read back in 2007 asked the rhetorical question: "If moisture testing is so accurate, why are we still having problems?" Fourteen years later, the problem has gotten worse. The most upsetting part of this is that almost all of these issues are completely avoidable—if you know what to look for. The tricky part is that the most common problems are those you can't see.
Unlearn to learn
First off, when teaching a class, I tell the attendees to basically forget the crap they've been taught, because most of it is based on a series of false precepts; and as long as these precepts remain in place, the problems CAN'T and WON'T go away. Let's take a look at two of these common false precepts.
False Precept #1: The moisture migrates from the bottom of the concrete and causes flooring failures.
In the 40-plus years I have been in this business, I can state with much certainty that the vast majority of on-grade moisture issues are NOT created by this "fact."
First off, concrete never dries … period. It can "dry" relative to its properties, but the water added to the concrete when it is freshly placed averages 6–7% moisture by volume, and the rest is sand, rock and cement. More than half of the mix water is retained in the concrete in any livable environment. Any moisture that "leaves" also tends to re-enter.
As for the water invading from underneath, that takes YEARS and, if there is a vapor retarder, maybe never. This follows a simple truism that every installer and inspector should know and understand: Water is incompressible.
Why is that important? Because concrete never dries. Water cannot pass through water. Any water trying to make its way through the concrete is blocked by the water already there! Note that this isn't the case for uncoated concrete, such as warehouses, garages, etc., which are a different subject matter altogether. This article is about concrete intended to be placed and have a flooring material installed over it.
False Precept #2: All moisture tests (measurements) are an indication of water originating from the concrete.
The vast majority of moisture measured usually originates from ambient conditions, not the concrete.
Because there are so many instances of failures occurring after the concrete was moisture tested (i.e., the floor failed due to high moisture readings at a later date) it has become the norm for many people to be holding their breath, waiting for the inevitable phone call about a problem.
First and foremost, with any currently available moisture reading, the measurements do not and cannot measure where the moisture originated. It has been assumed this moisture always originates from the concrete—wrong answer!
It has been long stated that moisture testing is accurate only at the time of testing, which is true. But it begs the question: Why aren't the site conditions being tested and monitored immediately before and during the flooring installation? That is when the majority of problems are introduced.
RELATED: Mitigate Moisture: Reduce Risk of Callbacks on Slab Jobs
The culprit: dew point and condensation
A couple years back, an installer called about a moisture problem he was having with his wood floor installation. He was very careful to conduct two different moisture tests—the moisture meter and the RH probe—and both indicated the concrete was safe to install over.
Within a couple days, he noticed some curling, so he removed the flooring in that area. He retested with the humidity probe and found the RH level had gone up. It was at 90%, and the moisture meter had also risen to higher levels than when he qualified the concrete and began the installation. The adhesive manufacturer informed him the moisture levels were too high, and he was on his own.
He tested the surrounding area, and the concrete humidity and moisture levels were the same as before the installation.
I asked him if he would be willing to try a different adhesive. Here is where it gets interesting: He stated he already had, and where he had used it, he did not see any of the problems he was experiencing with the original adhesive. I asked him to take his hygrometer and measure the ambient conditions of the job site and underneath the lid of each adhesive.
The ambient RH and the RH under the lid of the "successful" adhesive were at the same exact RH, whereas the adhesive where he experienced a failure indicated a RH of 90% (in the adhesive bucket)! It was a water-based adhesive and ended up being the source of the "mystery" moisture.
His claim against the original adhesive manufacturer ended up being successful because the company had failed to correctly instruct for site conditions where the concrete is significantly cooler than the air temperature.
This brings up the axiom: Moisture moves from warm to cool, so:
Everyday situations that introduce moisture to concrete
To help that installer in his presentation for the successful claim, I gave him the following photos and descriptions. They are everyday situations where moisture is introduced into the concrete.
The "mystery" moisture in one area of this floor was caused by a temperature difference; the colder concrete attracted so much moisture from the air every night that there was visible water on the floor.
Example #1: The area that wouldn't dry out
I was brought into this project to figure out why this area persisted in becoming wet, even after repeated drying. Each day it would dry it out, only to be soaking wet the following morning.
They tested for leaks, pipe breaks, etc., and spent considerable time and money trying to discover where this mysterious leak was coming from.
Using tools that I recommend to every installer, I measured the ambient conditions and the concrete surface temperature. The concrete temperature was consistent until I got close to the damp area immediately against the wall, which turned out to be an improperly insulated refrigerator.
The concrete temperature difference was almost 20°F colder immediately adjacent to the refrigerator wall. The concrete would attract moisture from the air overnight and by morning, it was soaking wet again.
RELATED: What to Do With a Wet Concrete Slab
The fix? I recommended they cut a channel ¾" deep and a minimum ½" wide into the concrete and place an insulative caulking compound into the freshly cut gap. This eliminated the temperature differential. Once the concrete near the refrigerator remained the same temperature as the rest of the concrete, it dried out.
Note that the gradient portion of concrete is typically between ¼ to ¾" in from the exposed surface. The gradient is the section of concrete that regularly participates in ambient changes, whereas the remainder of the concrete is somewhat consistent and subject to little change (unless over an uninsulated soil, or the underside is a surface of a suspended slab subject to a potentially different set of ambient conditions, which, again, is another subject that deserves its own article, particularly with non-conditioned sites).
They were a bit embarrassed about how simple and inexpensive the fix was, particularly after spending so much time and money.
When there is excess moisture on the floor, it doesn't necessarily come from below. That was the situation before the Nov. 30, 2016, NBA game between the Sacramento Kings and Philadelphia 76ers that was canceled (and even Kings star DeMarcus Cousins attempted to dry the court).
Example #2: An NBA game was canceled due to the flooring surface not being able to dry out.
Back in 2016 the Philadelphia Inquirer ran an article with the headline "76ers Postpone Home Game With Kings Due To Moisture On Court At Wells Fargo Center." The article went on to describe how the Nov. 30 game was first delayed and then canceled by the NBA due to "unsafe playing conditions on the arena floor."
There was "moisture on the court from the ice rink beneath the playing surface," as the temperature inside the arena was "higher than what it normally is for a basketball game." A Wells Fargo Center source said that someone in operations "dropped the ball and did not turn down the temperature in the arena." The Kings said they noticed there was a problem during their 10 a.m. shoot-around that day. It was noted that the arena felt humid, and the operations staff in the building had turned on the air conditioning in an attempt to cool the arena down. We'll have more on this problem after we go over Example #3.
RELATED: Six Essential Questions for Concrete Slab Prep
Example #3: Sweating slab syndrome
This is a very common problem, particularly with high-quality concrete where there is essentially no surface absorption of excess moisture. Day after day, as the other trades are working in the environment—one that has been previously tested, but still waiting for a flooring installation—it is amazing how much moisture can be introduced into the environment. With sweating slab syndrome, instead of this "unseen" moisture soaking into the concrete, it sits on top of the concrete (for more, see the sidebar below).
Moisture from the air: Where does it go?
Both the basketball court that is slippery from condensation and sweating slab syndrome are perfect examples of what an "unconditioned" ambient condition can create with all the moisture originating from the air. If the floor in those situations had been open uncoated concrete (after the testing had concluded but before the floor installation), rather than simply sweating on the wood or concrete surface, this moisture would have been absorbed, day after day after day.
In none of these situations was moisture "originating" from the concrete.
The truth is that this is where the vast majority of moisture problems originate—and every single one of these is easily correctable before and during a flooring installation. Yet installers and manufacturers alike are given a false sense of security by doing the qualification moisture testing … and then letting the chips fall where they may. They simply are not being taught these fundamental issues that could all but eliminate moisture claims with concrete.
I will rephrase the earlier rhetorical question: If current testing standards are so accurate, why are the problems getting worse, not better? In a future article, we will cover in detail just how easy it is to avoid these problems.
Sweating Slab SyndromeThese photos were taken by my colleague Steve Phillips at a recent project, and they show a phenomenon we refer to as "sweating slab syndrome." Moisture can accumulate when the concrete surface temperature nears dew point, particularly if the air temperature is warmer. This transient spike in moisture happens quite regularly in between the time the moisture tests are taken and when the project site conditions are approved, yet the concrete absorbs a damaging amount of moisture from the ambient conditions from a variety of different sources. |
A Rare Condition: Moisture From BelowThis photo is an example of an often misdiagnosed condition, both in causality and "apparent" pressure. When this epoxy coating was first breached, it made an impressive, if temporary "mini-geyser." This was mistakenly classified by the prior inspector as a continuous pressure, but it was actually "restrained" pressure. Once the restraint was gone, the geyser ceased. In a continuous pressure condition, the geyser would have remained to some extent, which is relatively common in underground structures. Other than random blisters, the epoxy was well-bonded. We extracted the liquid and found it to be highly alkaline (very concentrated), which caused damage to the epoxy/concrete bond line. This was NOT a case of surface condensation or dew point. This is a concrete, NOT flooring problem, yet the flooring contractor was being held accountable until my involvement. The prior inspector blamed the flooring contractor (while misdiagnosing the problem and giving incorrect repair advice), and this happens all the time. Fortunately, this condition is quite rare—unlike what is being taught and perpetuated to the flooring industry. According to the false precepts, the water originates from the bottom of the slab and migrates through. That is actually VERY rare, but it was the culprit in this situation due to the concrete slab originally being a warehouse that was never designed to be coated and had no vapor barrier. The slab was over 30 years old, which virtually guarantees this condition. |
This Is Essential: Verify Correct TestingThis is a case showing why all testing needs to be fully documented (photos, date stamped, site location, etc.). I was asked to go and review the calcium chloride testing conducted by a company that was "certified" by at least two schools/entities. When I got there I could see there appeared to be either a surface hardener/curing compound and/or primer that had not been removed (or even abraded) before testing. The project would have proceeded forward had I not visited. If the flooring installer had proceeded, they would have inherited the improperly tested concrete floor. Do not rely on undocumented testing—period. If the testing lacks proper documentation, it needs to be redone. If not, then anyone else who gets involved also has responsibility when things go south. |