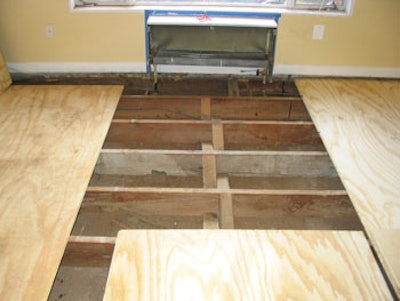
Flickr/omarali.md
Here are the common subfloors you'll deal with on the job and checklists to help you make sure the subfloors will be ready for your wood flooring installation. The following are general guidelines from NWFA's Installation Guidelines. For specific information, always follow the manufacturer's recommendations for the product you're installing.
Plywood and OSB Over Joists
Plywood and OSB subfloors over joists are most common in newer homes and new construction, typically in homes with basements or crawlspaces.
1) Suitable Wood Flooring: Any.
2) Thickness: Usually manufactured in 4-by-8-foot sheets, plywood panels and OSB are acceptable subfloors for hardwood flooring as long as they are the proper thickness. Keep in mind that for mechanically fastened floors, OSB doesn't hold fasteners as well as plywood, so you need to use a thicker material to get the same holding power. Generally, the minimum thickness for plywood is 5/8 inch; for OSB it's 23/32 inch. However, as joist spacing increases, the subfloors need to be thicker. For joist spacing of more than 16 inches up to 19.2 inches on center, the minimum thickness for both plywood and OSB is 3/4 inch. For joists spaced more than 19.2 inches on center, the minimum thickness for plywood is 7/8 inch and for OSB, 1 inch.
3) Check Before Installation: Once you determine the subfloor is the proper thickness, check that the subfloor is installed properly, with no issues that could affect your installation. Subfloor panels and fasteners should be properly placed according the panel manufacturer's specifications. If there are protruding fasteners, squeaks or loose panels, refasten the subfloor to the joists. The subfloor should also be clean and free of contaminants such as paint, sealer or drywall compound.
RELATED: Step by Step: Fixing an Uneven Wood Subfloor Before Wood Floors
Inspect the subfloor from below and note the direction of the joists. With the above specs, the flooring should be installed perpendicular to the floor joists. The flooring can be laid parallel to floor joists, but you may need to add a 1/2-inch layer of plywood diagonally or perpendicularly to the joists, or install a brace between the joists.
4) Flatness: Ensure the subfloor is flat to the recommended tolerances for the flooring you are installing. For installations using mechanical fasteners 1 1/2 inches and longer, subfloors should be within 1/4 inch in 10 feet or 3/16 inch in 6 feet. For glue-down installations and those using mechanical fasteners less than 1 1/2 inches, the subfloor should be within 3/16 inch in 10 feet or 1/8 in 6 feet. The subfloor can be flattened by sanding down the high areas or by installing shims such as roofing shingles or various thicknesses of plywood.
5) Moisture: Another critical part of the subfloor inspection process is checking the moisture content (MC) of the subfloor and joists. A moisture meter should be your best friend on the job. Whether you are using a pin or pinless model, make sure it is calibrated correctly for the species you are testing. (For more on moisture meters, see "Measuring Moisture".) Take several readings—a minimum of 20 per 1,000 square feet—and clearly document them. Many installers write the MC reading and date right on the subfloor, log them in the job-site notes and take digital photos for further documentation. If problems arise later, you may need to submit proof that you followed the correct procedures. For solid strip flooring, there should be no more than 4 percentage points' difference in MC between the subfloor and the flooring; solid plank flooring wider than 3 inches requires no more than 2 percentage points' difference.
Although moisture may be in check at the time of installation, it could slowly seep in through the wood subfloor and eventually into the wood flooring above. To help prevent this, an approved moisture-vapor retarder should be placed between the subfloor and the wood flooring. Approved vapor retarders include 15-pound asphalt felt paper, asphalt-laminated paper and 15-pound kraft paper. A vapor retarder material with a perm rating of 0.7 or less, such as polyfilm, can trap moisture in the wood subfloor and should not be used. Some manufacturers have their own recommendations for vapor barriers depending on which product you are installing, so always check with the flooring manufacturer first.
Particleboard
Particleboard is frequently discovered as a subfloor layer over plywood when carpeting or vinyl are ripped out.
1) Suitable Wood Flooring: Floating floors. Particleboard has no holding power for fasteners. Other wood floors may be installed if the particleboard is ripped out, but if the original subfloor is not thick enough, at least a 1/2-inch layer of plywood or 3/4-inch OSB must be added once the particleboard is removed. The other option is to install a layer of plywood or OSB over the top of the particleboard (although that may create unacceptable height differences with the adjoining rooms; always check).
Concrete Slabs
Concrete slabs are common in homes without basements, typically in the Southern and Southwestern regions of the United States. Below-grade areas of the home where the soil is 3 inches above the floor, such as walk-out basements, also have slabs.
1) Suitable Wood Flooring: There are several options for installing wood flooring over concrete. Always use the product and installation method recommended by the manufacturer.
• Directly Over Concrete: Floating floors, engineered floors, some solid strip and plank, and some parquet. Solid wood flooring is never recommended below grade, but some solid wood flooring manufacturers now recommend their products for glue-down over slabs. A vapor retarder is recommended any time you install a solid 3/4 –inch wood flooring over concrete.
• Over Concrete with a Wood Subfloor: Any.
• Over Concrete with Sleepers: Solid strip or plank can be laid directly over a sleeper system, but engineered wood flooring less than 3/4 inch thick or solid plank wider than 4 inches requires a wood subfloor over the sleepers. For obvious reasons, parquet cannot be installed over sleepers unless an additional layer of plywood or OSB is added.
2) Weight: There are different types and weights of concrete slabs, and not all are acceptable for glue-down installation of hardwood flooring. The slab must be a minimum of 3,000 psi; lightweight concrete is not acceptable unless you are installing a floating floor or a wood subfloor over the slab. A quick test is to drag a nail or other sharp object across the slab—if it leaves an impression, there's a good chance it's lightweight concrete.
RELATED: 5 Wood Flooring Installation Sins
3) Surface: As with all subfloors, inspect the surface of the slab for areas that can affect the flooring installation. The slab should be clean and free of contaminants such as sealers, waxes, drywall or paint. Slick slabs can prevent adhesive transfer, so areas may need to be abraded according to the adhesive manufacturer's recommendations. Also check for hollow spots, cracks and loose areas. You may need to grind down the slab or repair these problem areas.
4) Flatness: The slab should also be flat to the wood flooring manufacturer's specifications, usually 1/8 inch in a 10-foot radius. Mechanical methods for flattening the slab include grinding, bead-blasting or abrading. There are many self-leveling concrete compound products on the market, as well as patching compounds. The condition of the slab and products you are working with determine which methods to use. Always check with the flooring adhesive manufacturer to determine what is the best method to flatten the slab with the products you're using.
5) Moisture: As with plywood and OSB subfloors, moisture testing is one of the most important parts of your installation. Concrete is a porous material and can retain moisture and emit moisture vapor, which could end up in the wood floor above unless the proper precautions are taken. (For more on concrete subfloors, see "How to Get a Concrete Subfloor Ready for Wood Floors" in the February/March 2003 issue.) In new construction, the slab should be given at least 60 days to cure. No matter if it's new or old, or on or above grade, the slab should be thoroughly tested for moisture before any installation begins. Common concrete moisture testing methods include:
• Calcium-chloride test (ASTM F1869): measures the amount of moisture emitted from a 1,000-square-foot sample of slab surface in 60 to 72 hours.
• Concrete moisture meter: uses electrical impedance and electrical resistance to measure moisture in the slab.
• Phenolphthalein test: applied every 200 square feet in a job site.
• Relative humidity (RH) tests: measures RH by using either the Insitu Method (ASTM F-2170) or the RH Hood Method (ASTM F2420).
For solid wood products, a moisture barrier or vapor retarder is typically recommended. These include 6 to 8 mil polyethylene film applied over asphalt mastic, 15-pound felt applied over mastic and various other liquid sealants on the market specifically for concrete. Always check with the flooring, adhesive and moisture barrier manufacturers before installation to ensure that all products and methods you are using are compatible.
6) Additional subfloors: Depending on the product you're installing, you may need to install a wood subfloor over the slab. There are several methods, including:
• Floating subfloor: There are two common methods for this. The first is to lay two layers of 3/8-inch plywood over the slab without fastening or gluing them to the slab. One layer is laid, and the second layer is stapled or glued perpendicularly or diagonally over the top. The second method is to loose-lay one layer of 3/4 -inch plywood cut into 16-inch planks perpendicularly or diagonally to the direction of the flooring. The panels should be staggered every 2 feet and spaced 1/8 inch between ends.
• Glue-down subfloor: 5/8 -inch plywood panels are glued in a staggered joint pattern directly to the slab.
• Nail-down subfloor: 5/8 -inch or thicker plywood panels are fastened every 12 inches on center and every 6 inches along the border.
• Sleeper (screed) system – Common over radiant heat, this system has 2-by-4s spaced 12 inches apart. Solid strip or plank can be laid directly over a sleeper system, but engineered wood flooring less than 3/4 inch thick or solid plank wider than 4 inches requires a wood subfloor over the sleepers.
Whichever method you use for an additional subfloor, allow 3/4 -inch expansion space at the walls and vertical obstructions.
Older Subfloors
When you're walking into a remodeling situation, you never know what you will encounter on the job site. Removing existing floor covering can reveal many unpleasant surprises such as rotten boards, water damage, severe dips or humps, old adhesive or even mold. That is why it's important to do a thorough inspection from below from the basement or crawlspace. Common older subfloors include:
• Solid Wood Subfloor. This type of subfloor is common on older homes. As with plywood subfloors, if there is movement or squeaks, refasten the subfloor to the joists and set protruding fasteners into the subfloor. The boards should be no wider than 6 inches and installed on a 45-degree angle. If the subfloor is not acceptable, it can often be overlaid with 1/2 -inch plywood. Some wood flooring may not hold sufficiently if installed directly over solid wood subfloors. Engineered or solid strip flooring less than 1/2 -inch thick and parquet flooring may need an additional 3/8 -inch layer of plywood installed over these types of subfloors. Always check with the flooring manufacturer when in doubt.
• Existing Floor Covering. Whether it's vinyl, linoleum or an old wood floor, your best bet may be to install the new floor directly over the old one. You should never remove an old floor covering if you suspect asbestos was used. Older homes built before the 1950s often feature the infamous 9-by-9 tiles that contain asbestos. There were also vinyl tiles manufactured into the 1970s that contained asbestos. If you can't determine the age of the floor or are in doubt, for the safety of the crew and the occupants, have a sample tested before you rip out the floor. Any floor containing asbestos requires a professional abatement crew to remove the old floor.
Even if you know older floor covering doesn't contain dangerous contaminants, you may still want to leave it in place. For mechanically fastened floors, you can leave vinyl floor covering in place, and it will even act as a vapor barrier. However, for glue-down applications, you may need to remove vinyl or other floor covering, because they could affect the bonding of the adhesive, or they themselves may no longer be well-bonded with the subfloor. Always check with the adhesive manufacturer for its recommendation. If you leave existing floor covering in place, always check the height differences with floor coverings in adjoining rooms.
No matter which subfloor you are dealing with, you need to let everyone involved know what is needed for a successful wood flooring installation. Your customer may not see what is beneath the beautiful wood floor, but what you do below determines how the floor will look above. By following all the steps to prepare your subfloor, you create a solid foundation for your wood flooring.
Sources for this article included Rusty Swindoll, NWFA; Mickey Moore, NOFMA: The Wood Flooring Manufacturers Association; and Kevin Mullany, Benchmark Wood Floors Inc.