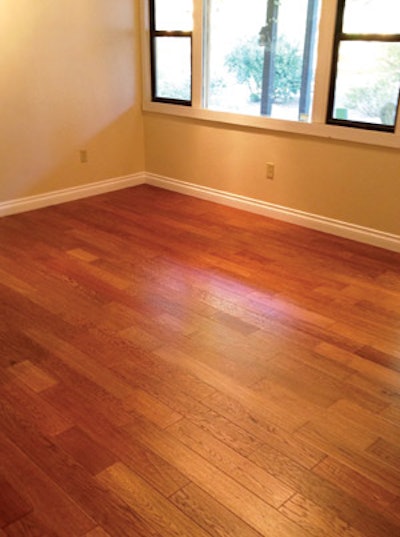
I started installing floors in 1979 and have seen our industry change over the years. When I bought my first set of tools from a guy who was retiring, my toolbox contained needle and thread for sewing carpet seams. Fortunately, it also came with a 3-inch seam iron. I only had occasion a couple times in my career where the needle and thread came in handy on a few sets of stairs. The last 15 years of my contracting career I have focused my business on hardwood installation and sanding and refinishing. There have been many changes here as well, such as the switch in the glues we use from high VOCs to water-based and urethanes. The primary method of installation has changed as well. Only 10 years ago, 90 percent of my business was glue-down prefinished hardwood. The occasional floating floor I did was usually an edge-glued laminate.
Today it has totally flipped, and now 90 percent of the floors I install are floating wood floors and laminates. Very seldom do I get to play in glue anymore, which is the good news, since the jobs go a little faster and my jeans look good longer. The drawback is that they can cost you money if you aren't careful. The biggest problem I have found is some of the floors are a little noisy underfoot when you walk on them. And the planks, once installed, can sometimes move and create gaps. Fortunately these problems can usually be avoided; here are what I have found to be the primary causes of these issues and how to prevent them.
Moisture & Movement
Edge-glued floating floors are typically engineered floors that are assembled with a bead of glue between the tongue and groove around the perimeter of each board. They are assembled over a 6-mil moisture barrier and a cushioned pad to reduce noise. These floors become one monolithic floor (basically, the entire floor becomes one piece). If you have an edge-glued floating floor that is making a lot of noise, chances are the issue is either floor prep or moisture. Let's take a look at each one.
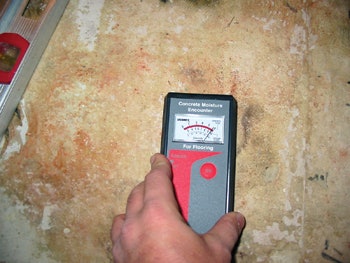
RELATED: Understanding How to Measure Moisture Can Avert Job-Site Disasters
If your glued-edge floating floor is making noise, one potential cause is that, due to moisture, the floor has expanded the maximum it can based on the expansion gap left during installation. At this point, the floor is locked in, hitting the walls or door jambs around the perimeter. You may notice that the floor seems a little softer or bouncier compared to what is was right after installation. This is because the floor is still trying to expand and now has no place to go but up. What you are hearing is the bond between the glued boards breaking as you walk across the floor. If you don't repair this quickly, the floor may begin to show separation and gaps between the boards. If that happens, the floor may not be able to be repaired, and replacement may be necessary.
If a subfloor like this one isn't flattened and cleaned, the resulting movement can break the bonds between the boards.
Note that when this happens, it's possible that the floor wasn't acclimated properly prior to installation. Or, it's possible the floor was acclimated properly but the temperature and moisture changed too much after installation. Be sure you educate customers about the importance of maintaining fairly consistent temperature and moisture in the home, and the fact that they should never completely turn off their heating or air-conditioning if they are leaving their home for extended periods of time. If they go on vacation or if it is a second home, they must maintain a minimum range to avoid drastic changes in temperature and humidity.
If debris like this is left on the floor, it can cause excess movement and noise when walked on.
Floor Prep Problems
If you have a noisy floating floor and you have removed all your moldings and baseboards and find there are still proper expansion gaps, you may have a floor prep issue. Floating wood floors typically require that the substrate, or subfloor, be flat to within a certain tolerance. This should be included in the directions that came with the product; NWFA Installation Guidelines say most manufacturers recommend a flatness tolerance of 1/8 inch in a 6-foot radius or 3/16 inch in a 10-foot radius. Making sure the subfloor is relatively flat minimizes vertical movement of the floor when people walk on it. Note, though, that with a floating floor you will always have a certain amount of movement, as it is installed over a pad. When you walk, the pad compresses and the floor will move. But too much movement-such as when the floorboards are spanning too big of a dip in the subfloor-can cause the floor to flex so much that the bond of the glue between boards will weaken. Over time, the bond can break, causing the floor to fail. If this is the case, you may be hearing loose boards beginning to rub against each other.
RELATED: Step by Step: How to Get a Concrete Slab Ready for Wood Floors
Even if the subfloor was properly flattened prior to installation, there is another floor prep issue that can cause noisy floating floors: There may be loose debris under the floor crunching as you walk. In either of these cases, whether the problem is an uneven subfloor or a dirty subfloor, there is not much you can do to fix the floor except pull it up and start over, making sure that the floor prep is done properly and the subfloor is clean of all loose dirt and debris.
Glueless Interlocking Issues
If the floor at issue is one of the newer glueless floating hardwood floors that lock together without adhesive, the cause of the noise may very well be the ones I discussed above: moisture or floor prep. But it's possible that the noise may also be inherent in the design of the locking mechanism of the floor itself. Let me be clear: That is certainly not true for every glueless floating floor. But over the last several years, as glueless floating floors have flooded the market, some manufacturers have rushed to keep up with others to secure their market share. As a consequence, I have found that some glueless floors will make noise no matter what you do.
As a contractor, I have seen my installation business change to where almost all the floating floors I install now are glueless-type installs. Some of these floors are easy to install and perform well, while others can be a nightmare. When I say "nightmare," what I mean is that it's all about customer expectations. I have personally installed thousands of square feet of these new products manufactured by almost every company in the business. If a customer is told at the point of sale that these floors tend to be a little noisier than glued floors, there is usually no problem. If they're not informed of that fact, the floor may not meet their expectations.
From my experience, in general, the wider the plank, the quieter the floor. I have found that a 3-inch wide board made by Manufacturer X sounded like walking on Rice Krispies, while the same floor from the same manufacturer in 5-inch was fairly quiet. What is causing the noise in some of these products is the fact that although the manufacturing tolerances of these products lock the boards together, there is some movement between boards, so they can squeak and make noise when walked upon.
RELATED: Engineered 101: Understand the Fundamentals of Engineered Wood Flooring
A couple years back I did an experiment on a job where I was installing 2,500 square feet of 3-inch-wide Product X. After installing the first room (approximately 250 square feet), every step was creaking and popping. The floor was properly acclimated and the floor was flattened and prepped to meet the manufacturer's requirements. At this point I had the homeowner walk on the floor, and he was not happy with the performance/noise the floor made when he walked on it. I pulled the floor completely up and re-flattened the subfloor so that it was completely flat, exceeding the manufacturer's requirements. I took photos and video of the subfloor prep and perfect flatness (just to protect myself) and then reinstalled the floor. Guess what? The floor sounded exactly the same-no change whatsoever.
Now, don't get me wrong, there is nothing wrong with these floors. They can be a great value for the money, and easier to install. They can just tend to be noisier than a glued or nailed-down hardwood floor. So, what can you do? In the example/experiment I mentioned above, I returned all the underlayment and kept the flooring but switched the customer over to a glue-down installation. This did not affect the warranty, as this particular floor could be floated or glued down directly to the slab. Once glued down, the floor had no movement and made no noise at all. It cost the customer the extra expense of adhesive and a little more in labor costs, but in the end he was happy with the installation and the floor looked great.
If you are looking at an installed floor with this problem, there are two things you can try to help minimize the noise:
1) If the problem is localized to a small area, a traditional fix is to try sprinkling a little talcum baby powder between the boards. Then gently tap the floor with a rubber mallet so as to not damage the wood. This will create vibrations, and the powder will migrate down between the boards. The powder will act as a lubricant and may solve the problem. Note that you should check with the manufacturer to make sure they approve this fix.
2) The nice thing about these floors is they can be disassembled and put back together at least three times, so if the problem is throughout the floor, you can pull it up and glue it down, or pull it up and edge-glue it. This will generally solve the problem, but it may affect the warranty, so check on this first. I would call the technical services department of the manufacturer and see if this can be done; ask them to send you an email verifying you can do this. If you don't get it in writing, you're leaving yourself open to a costly replacement.
Creeping Gaps
Something else I've noticed the last few years regarding floating floors is that sometimes they move due to foot traffic.
Something else I've noticed the last few years regarding floating floors is that sometimes they move due to foot traffic, exposing the expansion gaps. I have seen this most often at the pivot point of a hallway. For example, if the floor is installed in a hallway crossways (like the ties of a railroad track), each board is at most 3 to 4 feet wide. When the floor was first installed with a proper expansion gap on both sides of the hall and the gap was covered with baseboard or shoe moldings, it all looked great. Now there may be a board or two that is showing a gap between the edge of the floor and the molding. This happens very gradually and may not appear until several months after installation. The reason is that as the homeowner walks and turns to go down the hallway, the slight sideways pressure exerted by the pivoting foot creates a gap. The board(s) is moving a very slight amount each time, and eventually a small gap begins to appear.
RELATED: Why Flooring Straps Make My Life as an Installer Easier
This can be fixed a couple of different ways. The first is very simple-it may or may not work and is only temporary. Put on a pair of good sneakers that grip the floor and try kicking the boards back in place. If this does work, you may have to do it on occasion, as the problem will most likely reappear later. If you cannot get the gapping boards to move back into place using your foot, remove the baseboard on the wall opposite the gap, take a pry bar and gently pry the boards back to their original location. Again, this will most likely be only a temporary fix. To prevent the gaps from reoccurring, it will be necessary to disassemble the hallway back to the affected area and use some flooring glue (the type you would use on a glued-edge floating floor) between the tongue and groove and then reassemble. The glued boards will be able to withstand the sideways pivot pressure that caused the problem and this will be a permanent fix. Now remember, doing this may affect the warranty, so check first.
What Can You Do?
To prevent these issues from costing you headaches and money, there are a few things you can do. First make sure you have done the proper moisture testing recommended by the wood flooring manufacturer and have documented your testing. Never cheat on floor prep or acclimation, since most failures in our industry are related to either moisture or improper floor prep. If you pull up the existing floor and discover extensive prep is required but the customer is not willing to pay for repairs, do not do the install. Even if they tell you something like, "I don't care if the floor fails later-I'm just trying to sell the place," etc., do not do the job. If you install it, you own it. Even if you get it in writing that the customer was OK with you installing it that way, if you get sued later, you will lose in court. The judge will rule you were the professional and you should have known better. Plus, your name is on it, and you don't want your name out there associated with bad work.
Once you begin your floating install, check it after you have installed the first several rows. Walk on it back and forth, and if it's quiet, you're good to go. If it's noisy, stop and have the customer walk on it. Explain to them that they chose a great floor but that some floating floors are a little noisier than glued-down floors, and are they OK with the creaking? Some people will tell you that it's fine, because the old hardwood floors that they grew up with made noise and they expect it. If that's the case, keep going. If they tell you they were not expecting the floor to creak and they don't like it, stop and call the person who sold the floor. Most salespeople don't even know that noise with floating installs is a potential issue. If you don't stop but instead finish the install and your customer ends up being unhappy, he or she will call you or the retailer. The retailer will call the manufacturer, and they will send out a company inspector. Best to avoid this scenario entirely by making the customer happy up-front.
As technology changes, you've got to keep up. Try to attend as many manufacturer training classes as you possibly can when they are in your area. Make sure you schedule time to bring everyone in your crew as well; they need first-hand training as much as you do. Also be sure your subscription to Hardwood Floors is up to date. Make sure you know about all the latest changes that may affect your business as the industry moves forward.