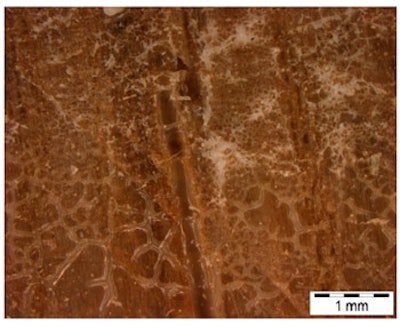
As engineered wood flooring becomes more prevalent, we are seeing increasing numbers of cases of delamination, especially under the extremes of dry or wet climatic conditions. Here in Germany, oftentimes floor heating is involved, and an increasing number of incidents are also observed after renovations with waterborne coatings. This led us to do some testing of these products in the lab, with somewhat surprising results.
What Can Floors Withstand?
In Germany, no regulations for the quality of the bonding between the layers of engineered wood floors exist, but we do have recommendations from flooring associations and manufacturers for the required humidity during usage: Often between 50 to 60% relative humidity is the recommended range. In the case of floor heating, the recommended maximum surface temperature ranges between 77 and 84 degrees Fahrenheit (25-29 degrees Celcius).
For experts having to determine the cause of delamination of engineered hardwood, the situation is not easy. In most cases, climatic conditions exceeding the recommended guidelines can be measured or at least estimated. But are climate extremes always the real cause? What if the material had substantial weaknesses that only become visible because of the extreme climatic conditions? How are we to detect or to exclude these defects if standards and requirements are nonexistent? Which climate extremes can common engineered wood floors withstand without failure?
At the Fraunhofer Institute for Wood Research (WKI) we have done some basic work on that question.
The Engineered Experiment
Eighteen different engineered hardwood floors were glued on a subfloor with warm-water radiant floor heating within a climate chamber. The different floors were conventional market products ranging from low-budget quality to the upper end of the price range. Thirteen wood floors had a top layer of white oak and five had a beech top layer. Thirteen were bonded with urea-formaldehyde resin (UF) and five with polyvinylacetat (PVAc).Three panels 300 mm (11.8 inches) long were assembled for every floor, with an additional half panel on each side.
There were two phases of the experiment. In the first, the RH was 35%, and the surface temperature of the floor was increased stepwise. These conditions may be regarded as rather mild. After this phase the floors were left without climate regulation-the doors were opened so the chamber could adjust to the ambient conditions.
In the second phase, an initial surface temperature of 86 degrees Fahrenheit (30 degrees Celcius) and 24% RH for 17 days was followed by a RH of only 14% for 22 days. These conditions may be regarded as rather severe and clearly are beyond the recommendations for wood floors.
Despite these extreme climatic conditions, no delamination was observed in any of the 18 floors. Only some minor cracks in the wood and some opening of joints within the top layer of the flooring became visible.
Surprising Results?
It became obvious that 18 engineered wood floors typical in the German market are able to withstand a significant deviation of the recommended moisture level and an extreme beyond the recommended surface temperature.
This rather tolerant behavior of engineered hardwood flooring is not really surprising. The glues used for the floors are common and have been established for decades. Both may be sensitive to long-term moisture exposure, but with both types a long-lasting bond between most wood species is possible when appropriate care is taken during the bonding process.
According to the present knowledge, it is expected that engineered wood flooring of appropriate quality never fails due to debonding before serious cracking of the wood, pronounced cupping and large gaps occur. This view is supported by the fact that in most cases of delamination of hardwood flooring investigated at the WKI, shortcomings in the production process were found to be the cause of the damages. These failures range from partial missing glue, partially to low bonding pressure, a specific type of glue with the tendency to lose adhesion after years and too high residual concentration of ammonia in smoked oak, causing insufficient bonding with a polyurethane.
The preliminary test results and our experts' experience with delamination of hardwood floors in no way imply that the climatic conditions recommended by the manufacturer should be exceeded. The recommendations are justified to prevent gaps, cracks, cupping and other moisture-related problems of wooden floors. (As long as they are in a reasonable range and not only meant to have the possibility of making the customer responsible for each and every problem). But as a guideline for the assessments of debonding, our experiment would lead us to conclude that these recommendations seem to be of limited use.
Additional online-only copy from this article:
Looking for Failure Causes
In some cases when looking at delamination, a systematic investigation may show severe weaknesses of the material. In some cases, the underlying reason for debonding is easy to detect. In the simplest case there is no glue at all in the debonded areas.
If the glue is missing in some areas, or the glue beads have not been flattened during pressing, deficits at production level must be assumed. The photos below show a cross section and a view from above after removal of the top layer of a delaminated wood floor. From the left to the right of this oak flooring, a reduced flattening of the glue beads can be observed. The flattening of the beads corresponds with the adhesion intensity (or quality) of the top layer. The top layer breaks within the wood only where the beads are completely flattened.
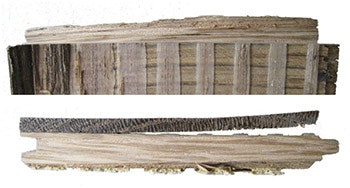
A typical structure of the glue that is referred to as "honey bread structure" also leads the diagnosis in the direction of production problems. It gets its name from what the structure you observe after picking up a slice of bread with honey or syrup that has fallen on the floor with the honey side down:
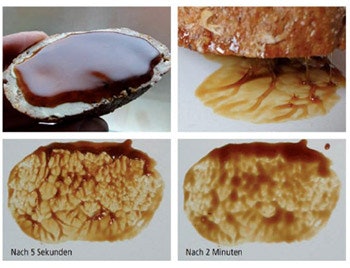
This problem is visible in wood flooring adhesive in this photo:
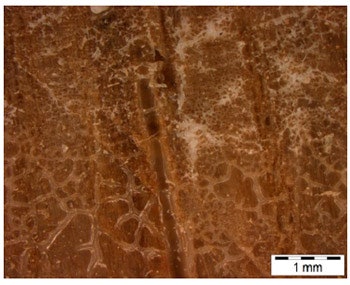
You can see the honey bread structure in the glue on the backside of a debonded top layer of an engineered hardwood floor. This same structure results when the pressure of a wood flooring press is released before the glue has completely hardened, so it demonstrates that the debonding took place during the production process. In the case of hot melts and thermoplastic PVAc, these honey bread structures may also occur after the production, but only in the less likely case of a subsequent surpass of the softening temperature of these glues.