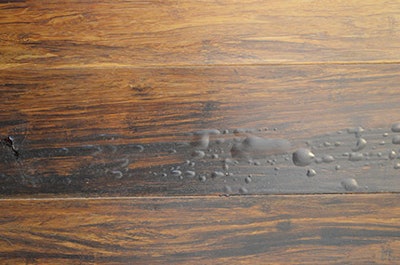
As inspectors, we are asked to go out and look at problems every day, and over the last couple of years, I have noticed an increase in moisture-related problems in concrete substrates. The issues I am referring to are not from new construction or even construction that is 20 years old; they seem to be more predominant in slabs from around the 1980s or older. Old subdivisions with tract-style homes and areas with high water tables appear to have the highest percentage of the problems.
What I find on these calls is sporadic dark discoloration and/or opaque bubbles appearing in the engineered or solid hardwood flooring. For example, entering the home, I notice two or three of these areas in the living room, one in the master bedroom and dining room and two in the guest bedroom. The remainder of the hardwood flooring has no issues. The first thing that comes to mind is moisture, but I find the areas affected are not around water sources. I proceed to take moisture readings and find the problem areas have high moisture readings, but the unaffected areas are within normal regional limits. What's causing the discoloration or opaque bubbles?
Oftentimes, during the investigation, I find out that the house was built in the late 1970s, and 1,000 square feet of ½-inch prefinished solid oak flooring was installed. The installer is present and shows documentation of his calcium chloride test results of three test locations, which all measured below 4 pounds MVER. The adhesive used is recommended for up to 8 pounds MVER, and the moisture content readings of the hardwood flooring were at the EMC of the home at the time of installation. The installer removes planks from both the discolored and unaffected areas, and I find the coverage rate of the adhesive is per the manufacturer's guidelines. All the evidence so far shows the installer followed all the necessary guidelines to have a successful installation. So, is the installer at fault for the failure?
In this scenario, sometimes the homeowner has hired a leak detection service before my arrival, and the results show there were no leaks. Now let's take the facts one step at a time:
This moisture migration can manifest as bubbles/blisters in the flooring surface (above), and/or dark areas in some boards (bottom photo).
1) We know the moisture content of the hardwood flooring was at EMC, so there is no problem there.
2) We know the calcium chloride results were below the adhesive's limitations, and the coverage rate was achieved, so, again, no problem there.
3) The leak detection service found no leaks, and there were no signs of leaks before installation, so no problem there.
The facts show the installer is not at fault, and this is a site-related problem, but yet some inspectors will blame the installer.
RELATED: Avoid These Mistakes When Moisture Testing Wood Floors
So, where is the moisture coming from? The only source left is the concrete substrate, but how? The calcium chloride tests were acceptable, and the installer performed them in three random locations per the standard ASTM 1869. But let's say (for the sake of this article) one test equals 1 square foot, so only 3 square feet out of 1,000 was tested—that is less than 0.3 percent of the total job, or, in other words, 99.7 percent was not tested. The odds of testing in the problem areas are pretty slim. Through my experiences taking numerous core samples to view the conditions below the slabs on these jobs, I've found the problem is occurring with the polyethylene sheeting—it has holes and is brittle or degraded, if not entirely broken down. The polyethylene from this era was the best technology of the time for preventing moisture from migrating into the floor covering, but it's coming to the end of its effectiveness.
Most, if not all, insurance companies have "property exclusions" in their policies that will not cover moisture-related damage of this type. For example, a general statement may be, "Water below the surface of the ground, including that which exerts pressure on, or seeps or leaks through a building, wall, bulkhead, sidewalk, driveway, foundation, swimming pool, hot tub or spa, including their filtration and circulation systems, or other structures, are not covered."
RELATED: Understanding How to Measure Moisture Can Avert Job-Site Disasters
How can installers or retailers protect themselves from such a scenario? The first course of action is to complete a thorough site evaluation of the home or facility. Is the landscaping flowing away or toward the home? Is the landscaping below the slab? Does the home have a musty or wet smell? Ask questions, such as when was the home was built, what kind of floor covering was installed (if not visually evident) and if they had any water-related damage. Take several moisture readings and record them, even if they do not show an elevated level. Inform the customer that due to the age of the home, there is a possibility that installing a wood floor could reveal an underlying problem. Let them know you recommend a moisture remediation system, such as a one-step adhesive, two-part adhesive system or even an epoxy system that can handle elevated moisture vapor emissions. Let them know you are taking every effort to have a successful installation.
On the legal side of things, examine your contract. Before starting any job, every installer or retailer should have a contract that includes provisions for this type of failure. Here is an example: "It is hereby mutually agreed that the Contractor shall not be held responsible or liable for any monetary loss, damages or inconveniences from underlying moisture emissions not detected at the time of installation, that all efforts have been made to detect such a problem, and are therefore not warranted."
Unfortunately, in today's society, there are people who are always looking for a way to litigate a problem, and this has gotten worse over the years. In order to help protect yourself, remember (as with any successful installation), it all starts with prep work. Conduct thorough job-site evaluations, complete quantified moisture tests, follow the manufacturer guidelines, have proper contracts and document everything.